Our die factory is fully equipped to produce pinch pointing drilling point dies that exceed customer expectations. Being not only a OEM/ODM factory but also heavily invested in developing our own brand, our expertise extend to not only the manufacturing side, but also on the practical side. Where most die manufactures make changes only according to customer drawings or indirect feedback, Broaden constantly receives first-hand feedback from distributors, dealers, end-users and on-site workers from projects big and small, which enables us to make changes and improvements that work not only on paper, but in the field!
Situated on a 700 square meter space, our pinch pointing die manufacturing site are fully equipped with the following equipment:
Equipement
A horizontal-spindle surface grinder is a used to achieve flat surfaces on a workpiece. The grinding wheel is positioned horizontally, parallel to the worktable allowing the machine to grind the surface of the workpiece with a side-to-side motion.
Similar to the Semi-Automatic Surface Grinder and differs only that an operator is responsible for manually moving the worktable, adjusting the crossfeed and downfeed, and controlling the engagement of the grinding wheel with the workpiece.
A Vertical Turret Milling Machine has a vertically oriented spindle, which is mounted on a turret. The turret is a rotating platform located above the worktable, which allows the spindle to move in multiple directions to perform various milling operations.
Our hydraulic compression molding press are used combine the pinch pointing die to base.
also known as spark machining, spark eroding, die sinking, wire burning or wire erosion, is a metal fabrication process whereby a desired shape is obtained by using electrical discharges (sparks). Material is removed from the work piece by a series of rapidly recurring current discharges between two electrodes, separated by a dielectric liquid and subject to an electric voltage. One of the electrodes is called the tool-electrode, or simply the tool or electrode, while the other is called the workpiece-electrode, or work piece. The process depends upon the tool and work piece not making physical contact. Extremely hard materials like carbides, ceramics, titanium alloys and heat-treated tool steels that are very difficult to machine using conventional machining can be precisely machined by EDM.
Our abrasive blasting process is perfomed in a closed loop cabinet system, which unlike conventional blast pots, allow operators to blast the workpiece, while keeping the spent abrasive contained inside. This protect the operators and surrounding area while enabling the recycling and reuse of the abrasive elements. We utilize abrasive blasting cabinets to further abrade, modify, polish and refine the tooling dies surface.
Our 3-Axis Automatic Surface Grinder is used when a smooth finish is required on larger flat surfaces areas. With 3-Axis, complex and precise grinding can be performed without sacrificing efficiency, and overall quality of the surface can be easily achieved.
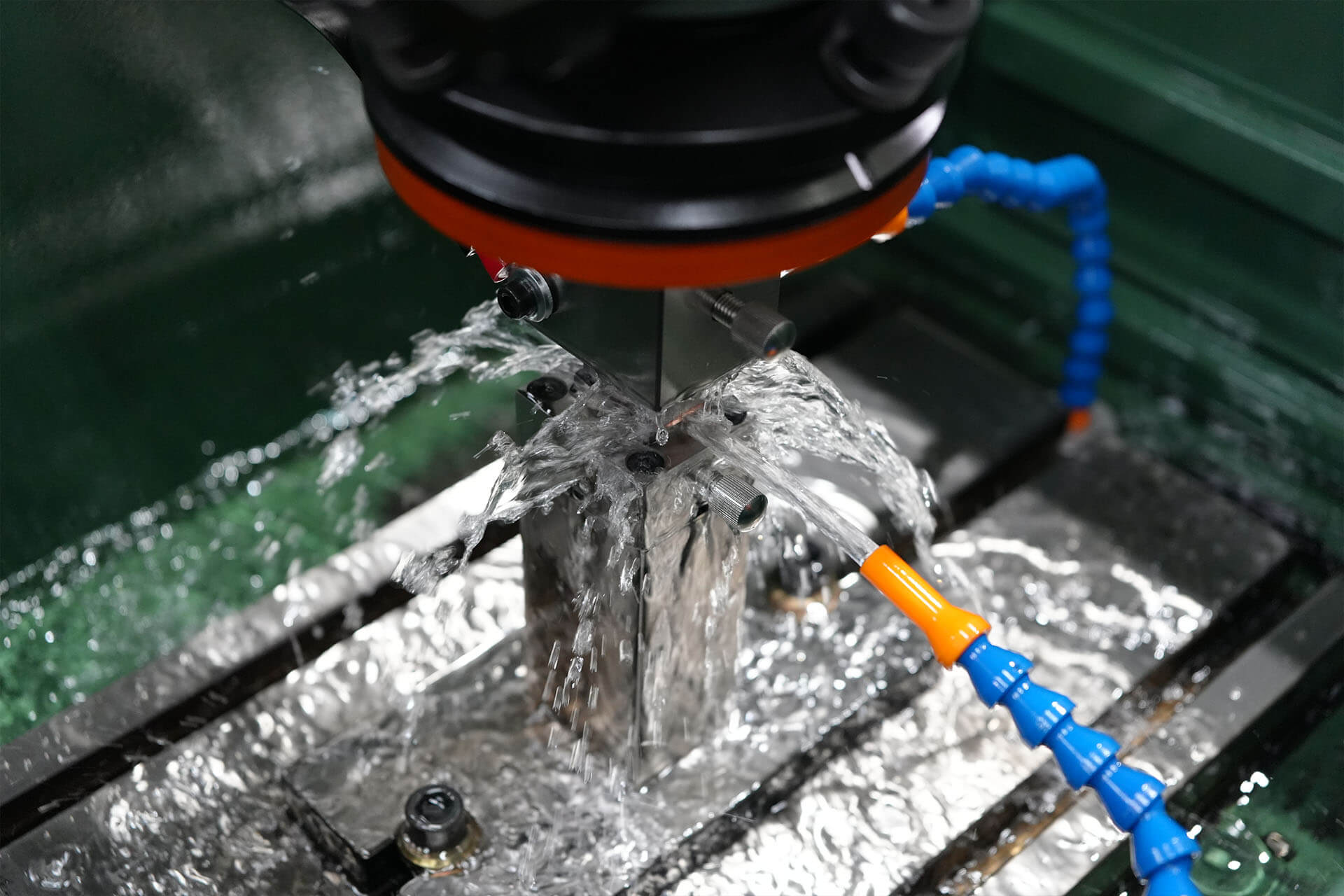
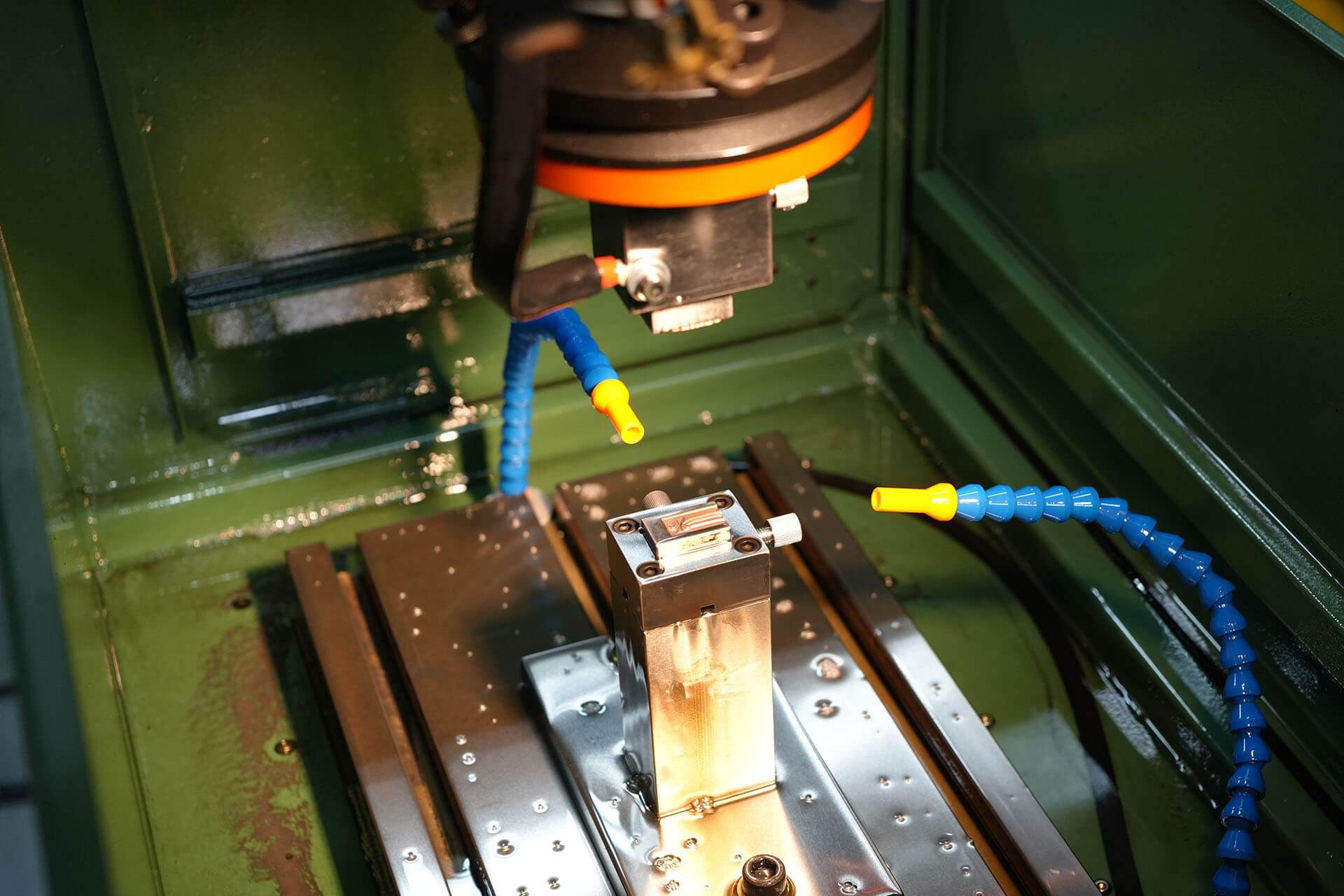
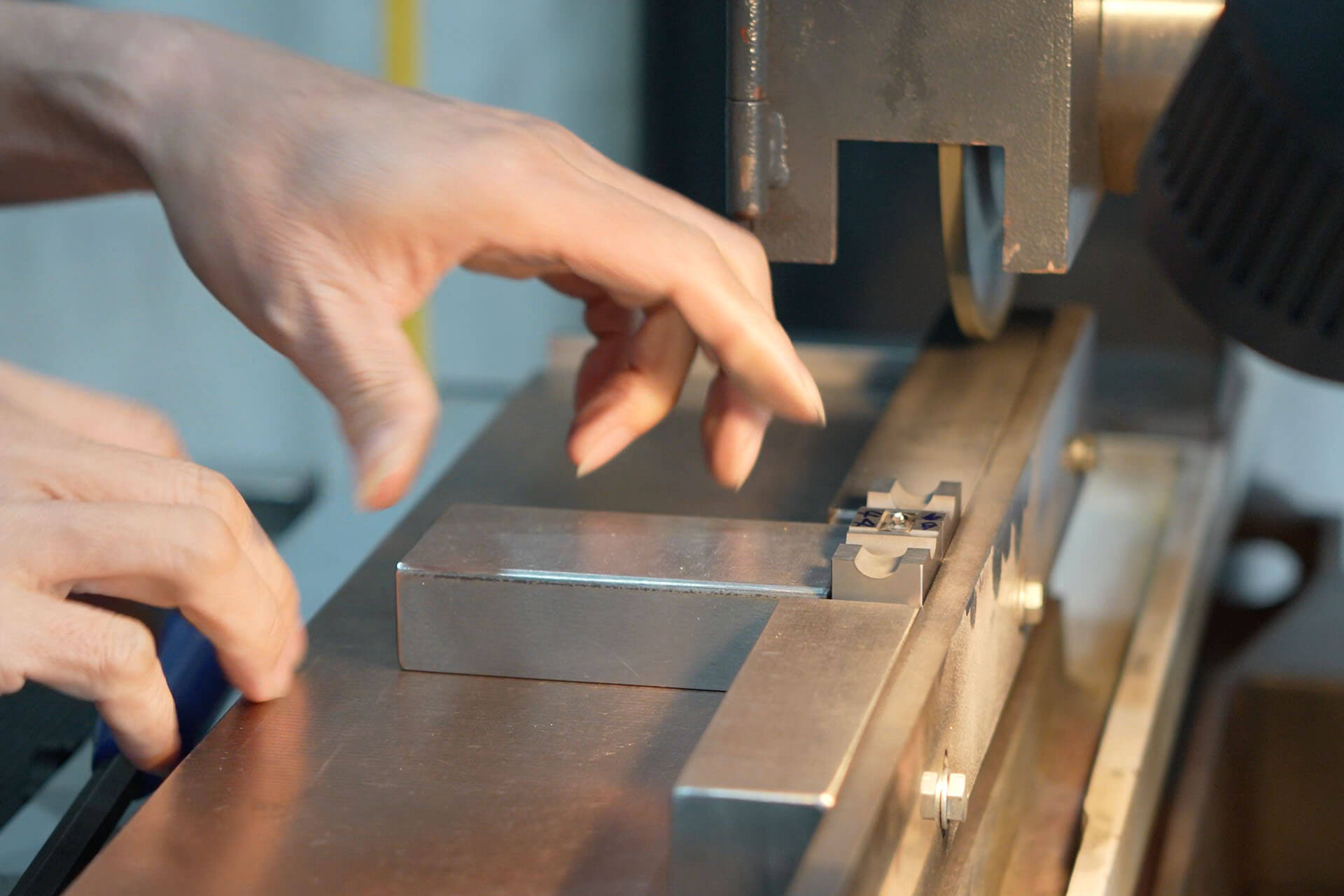
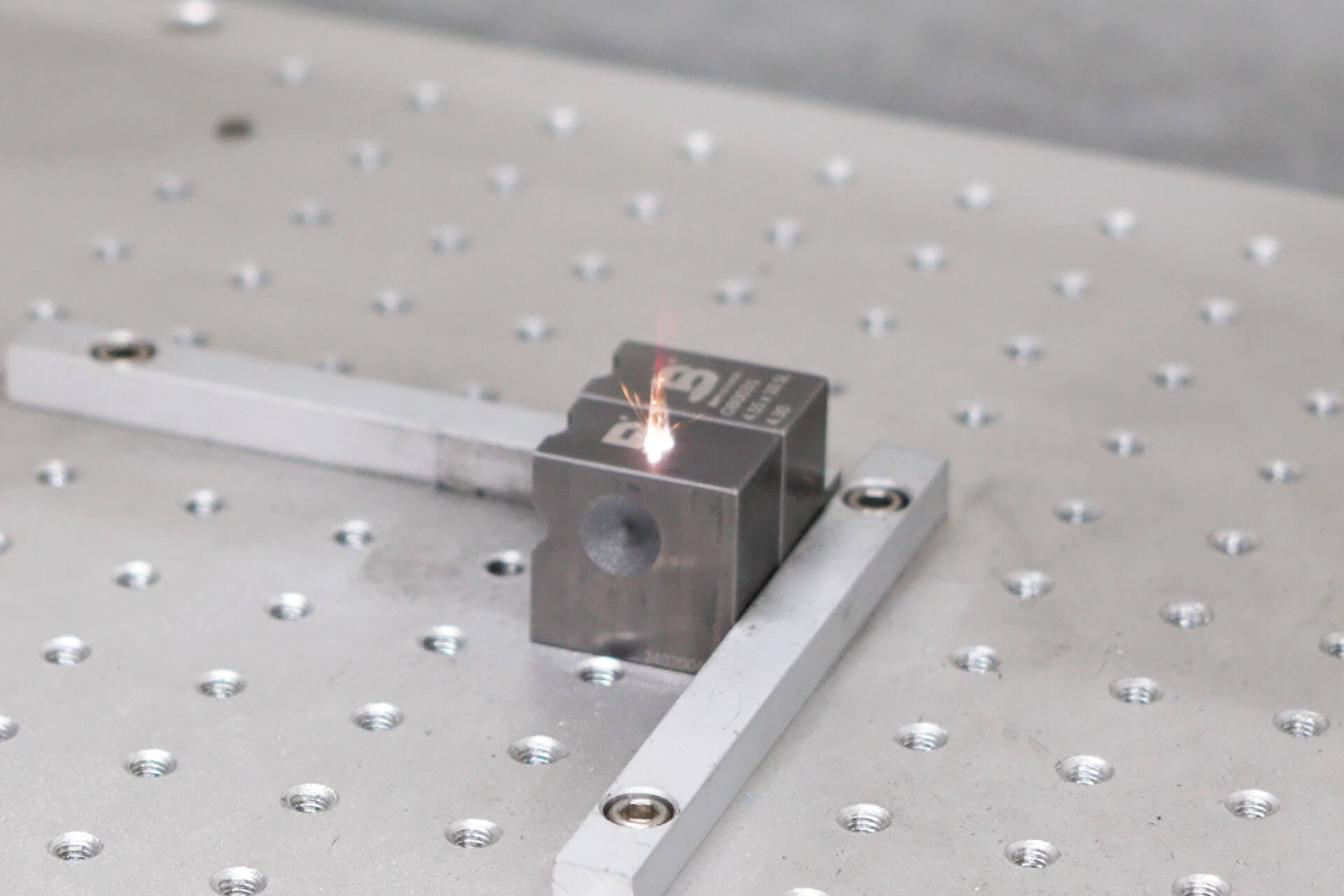
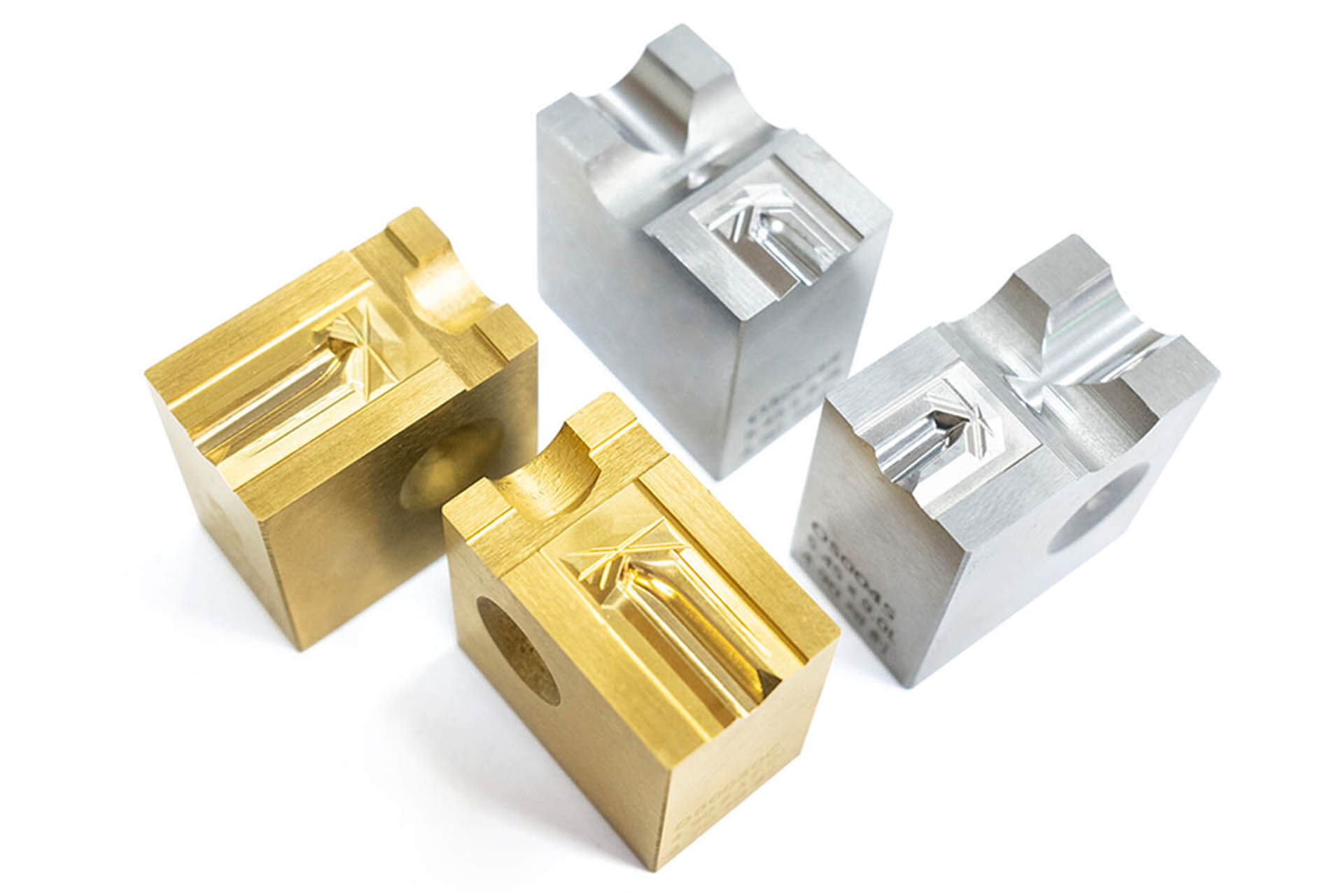
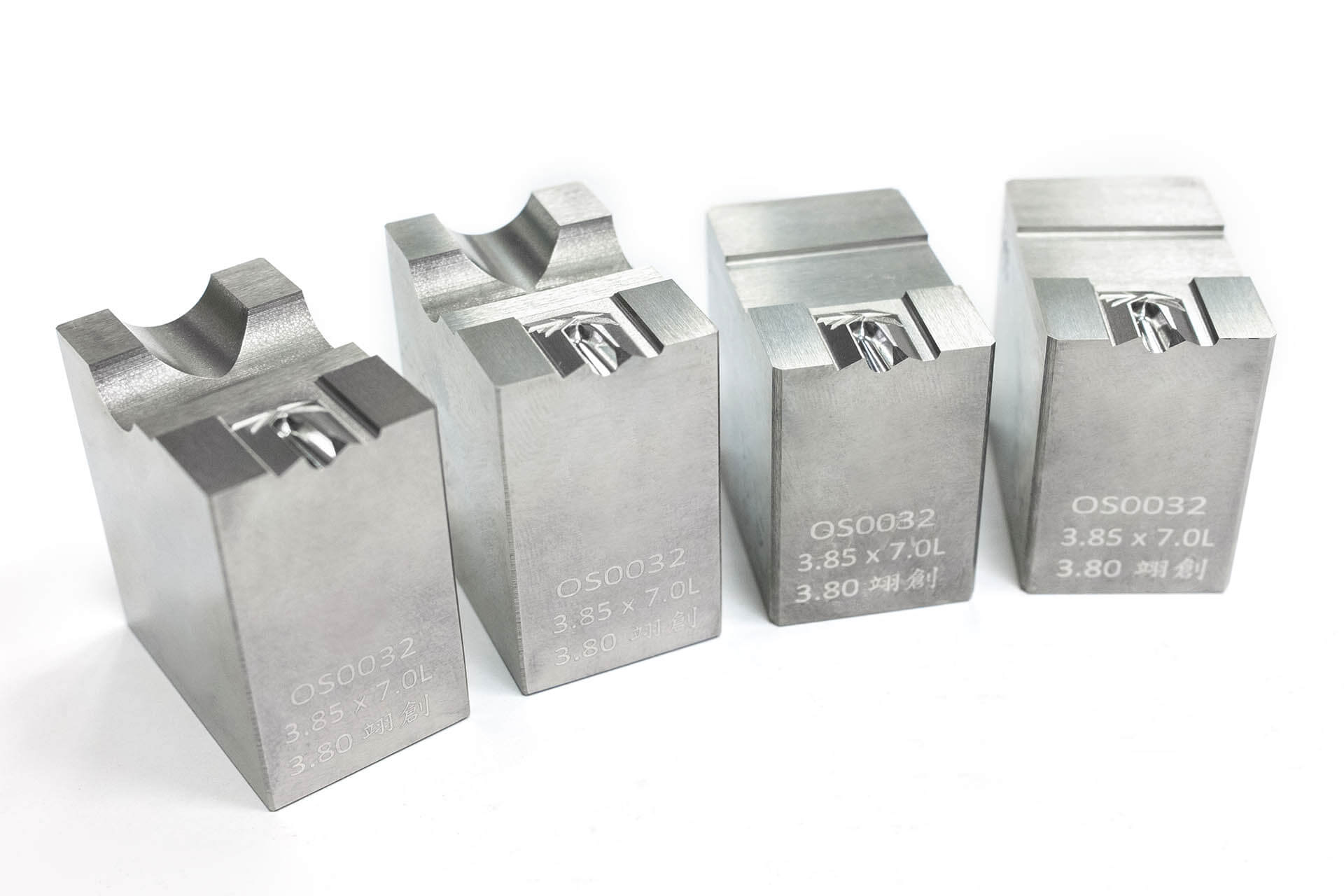
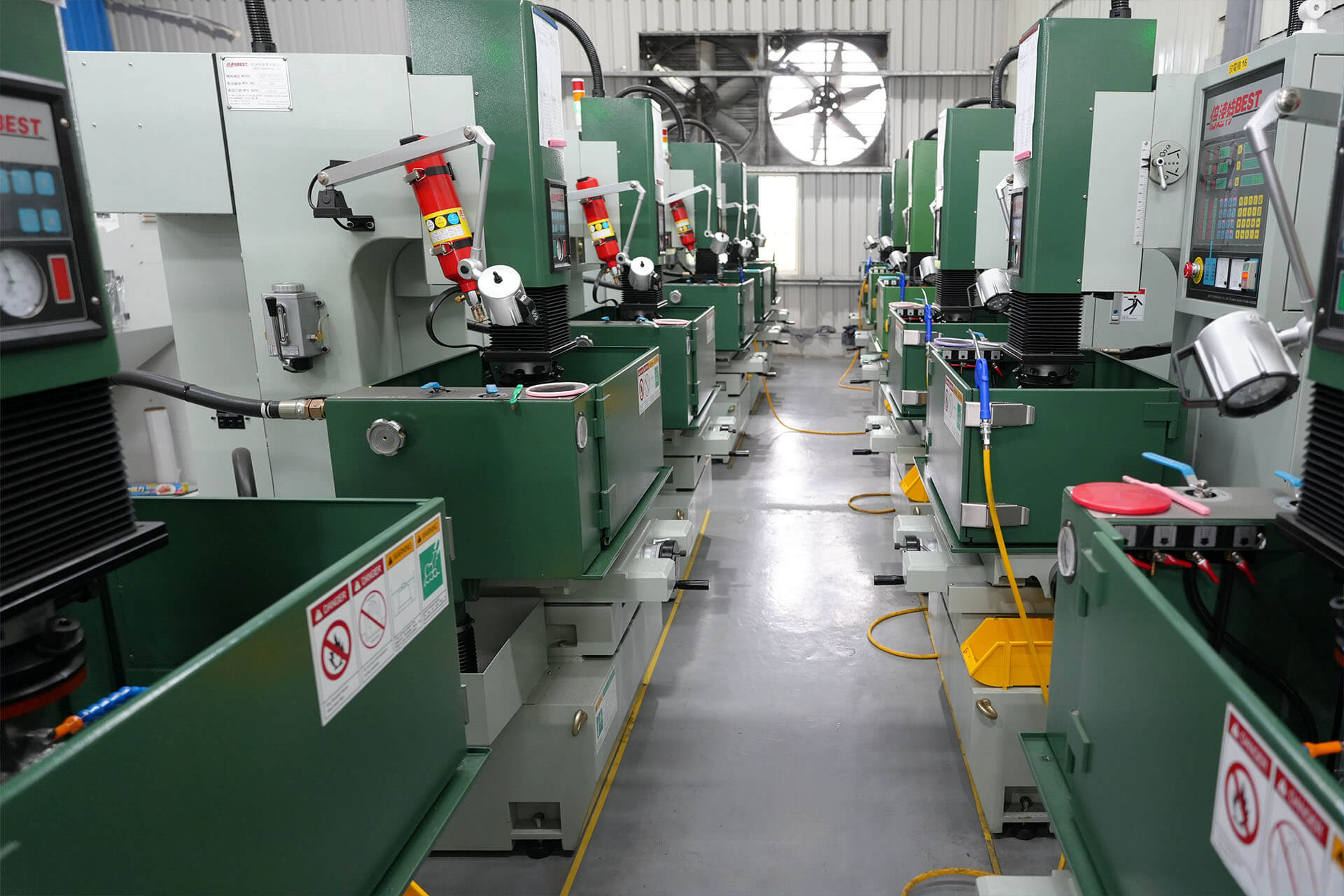
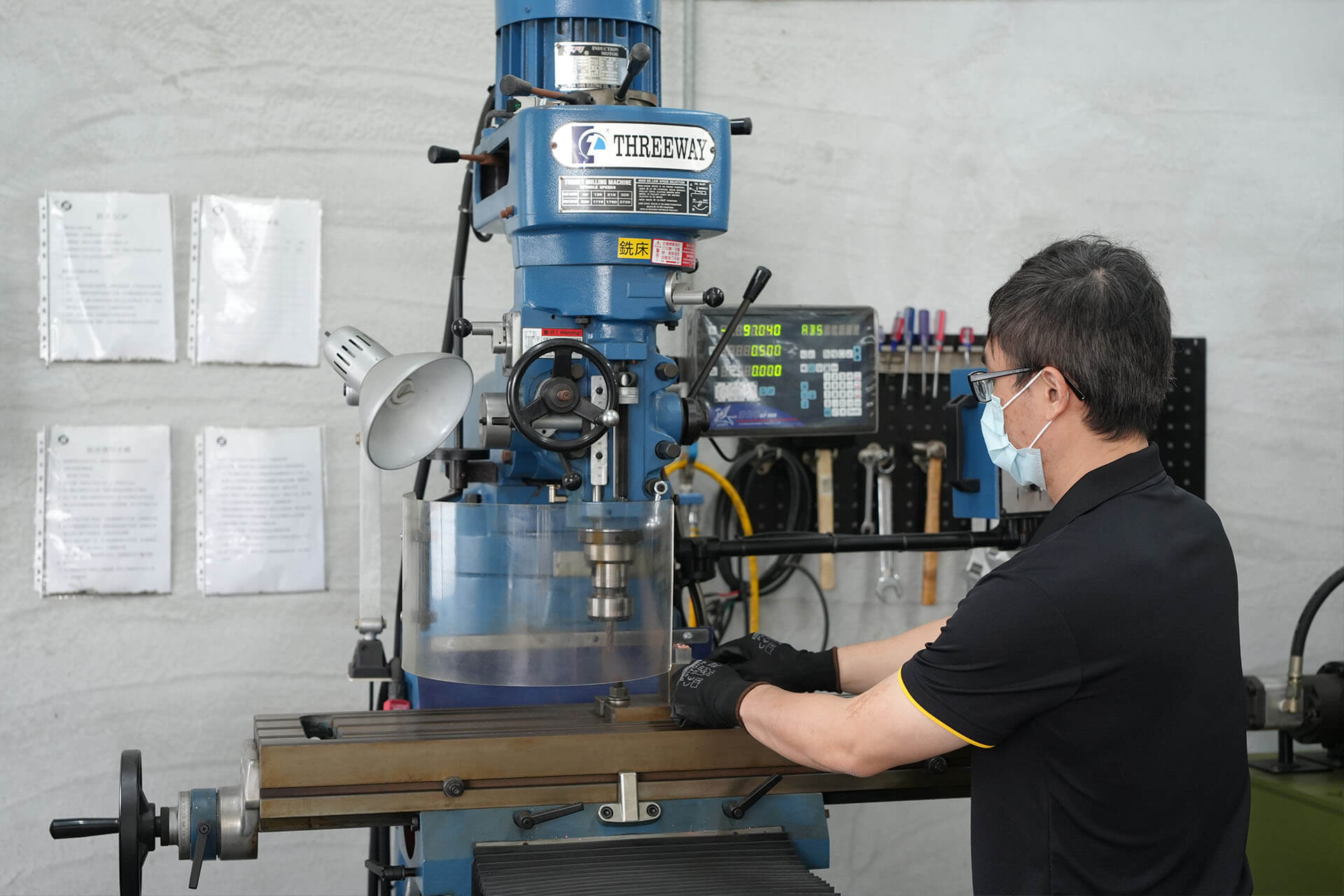
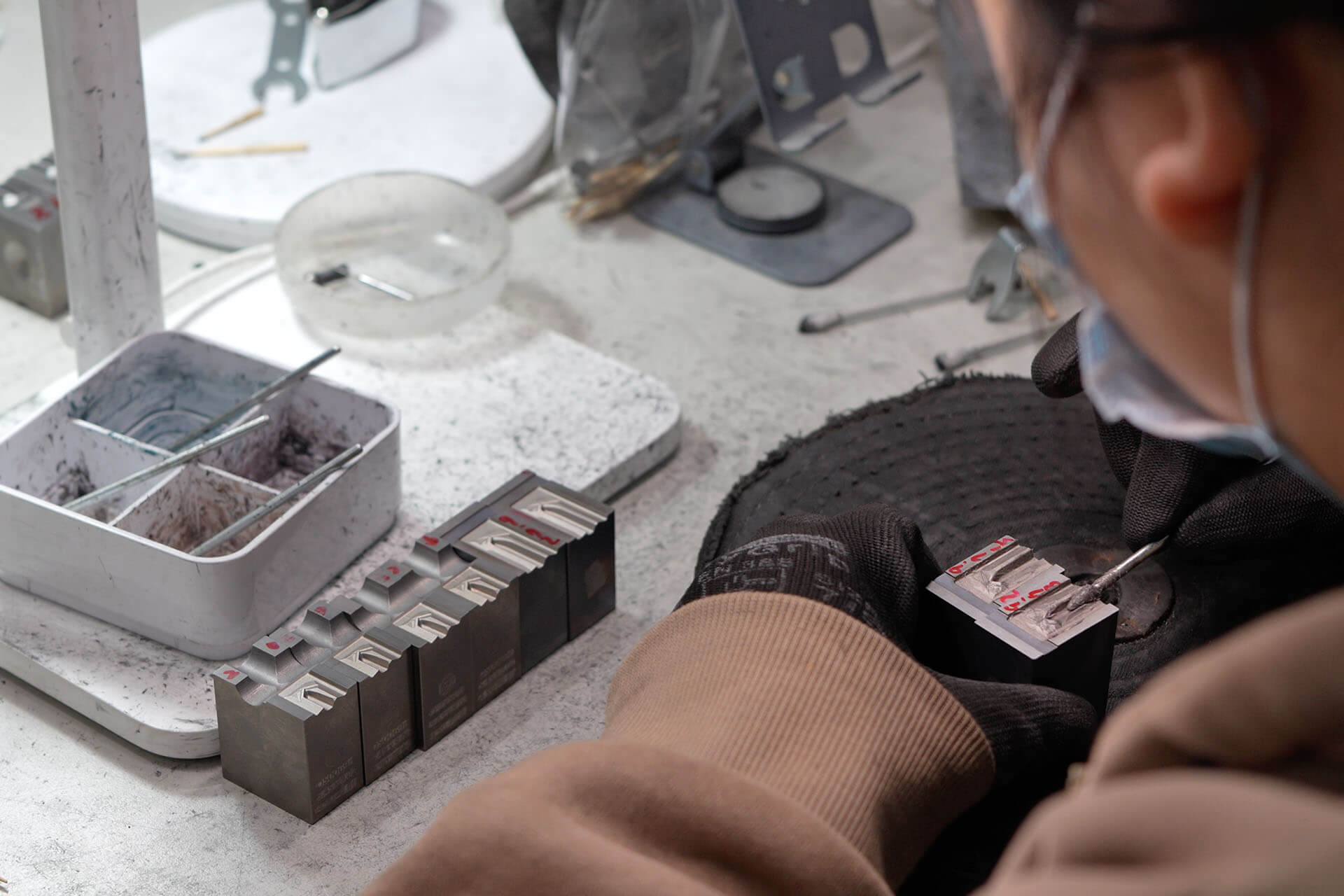
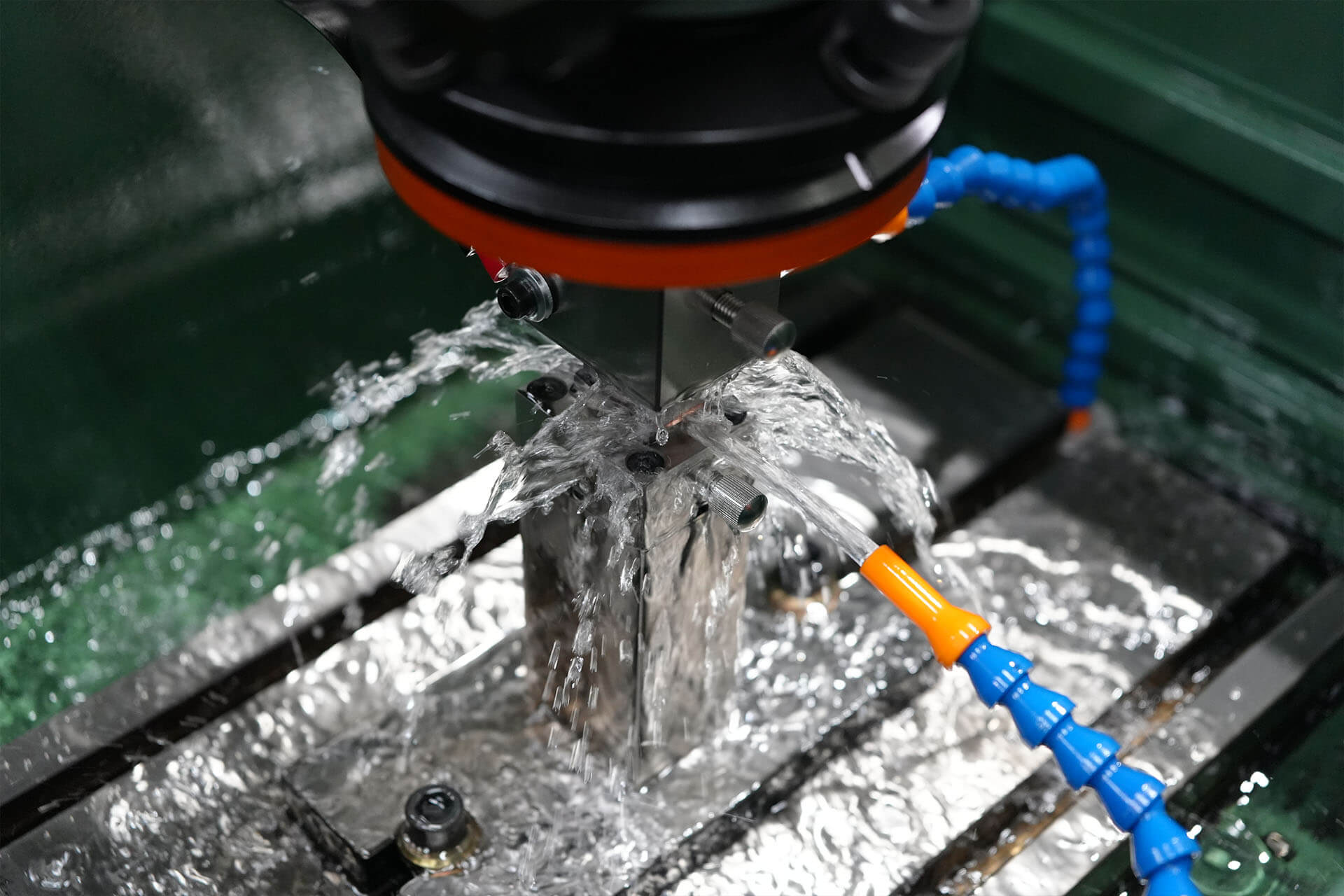
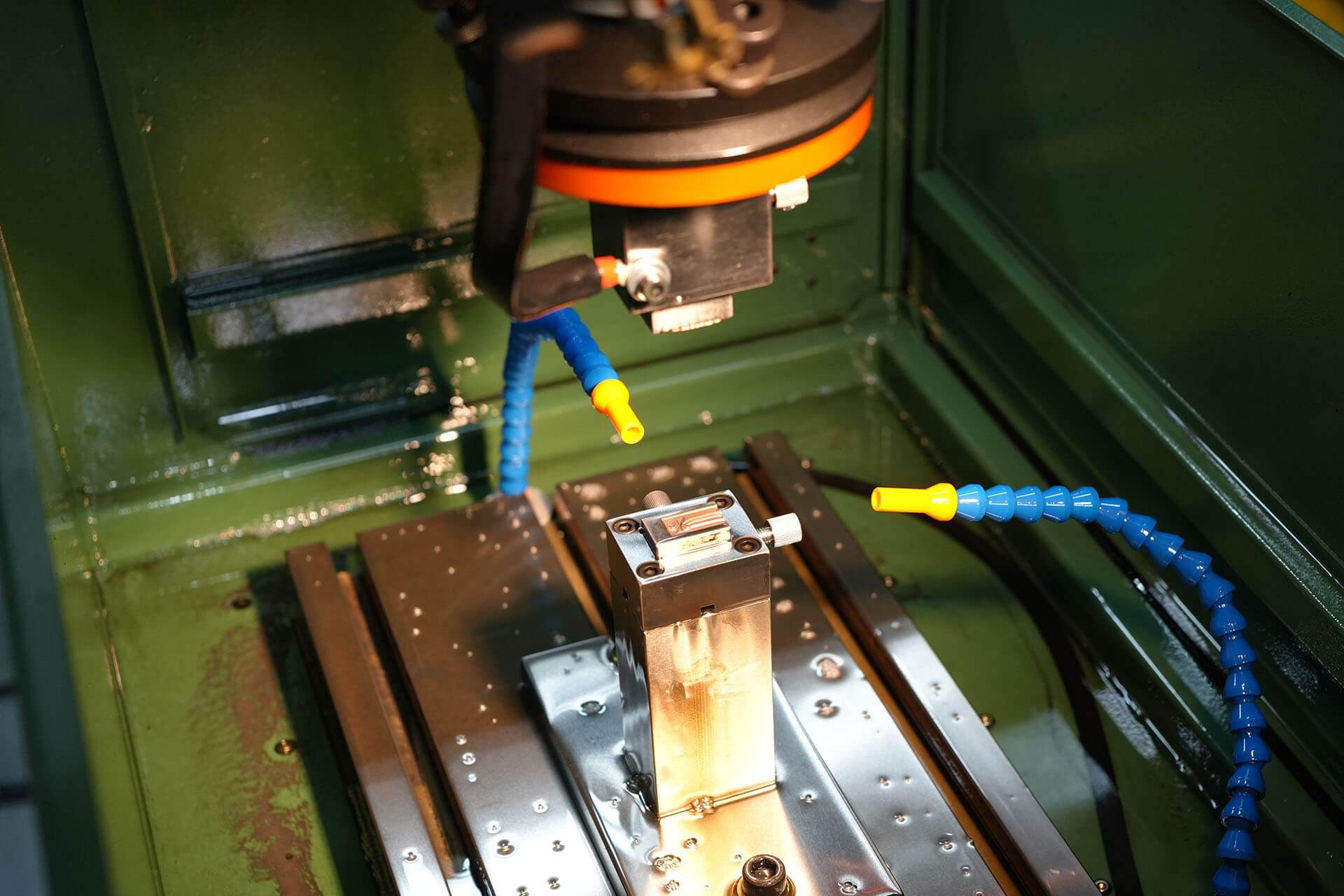
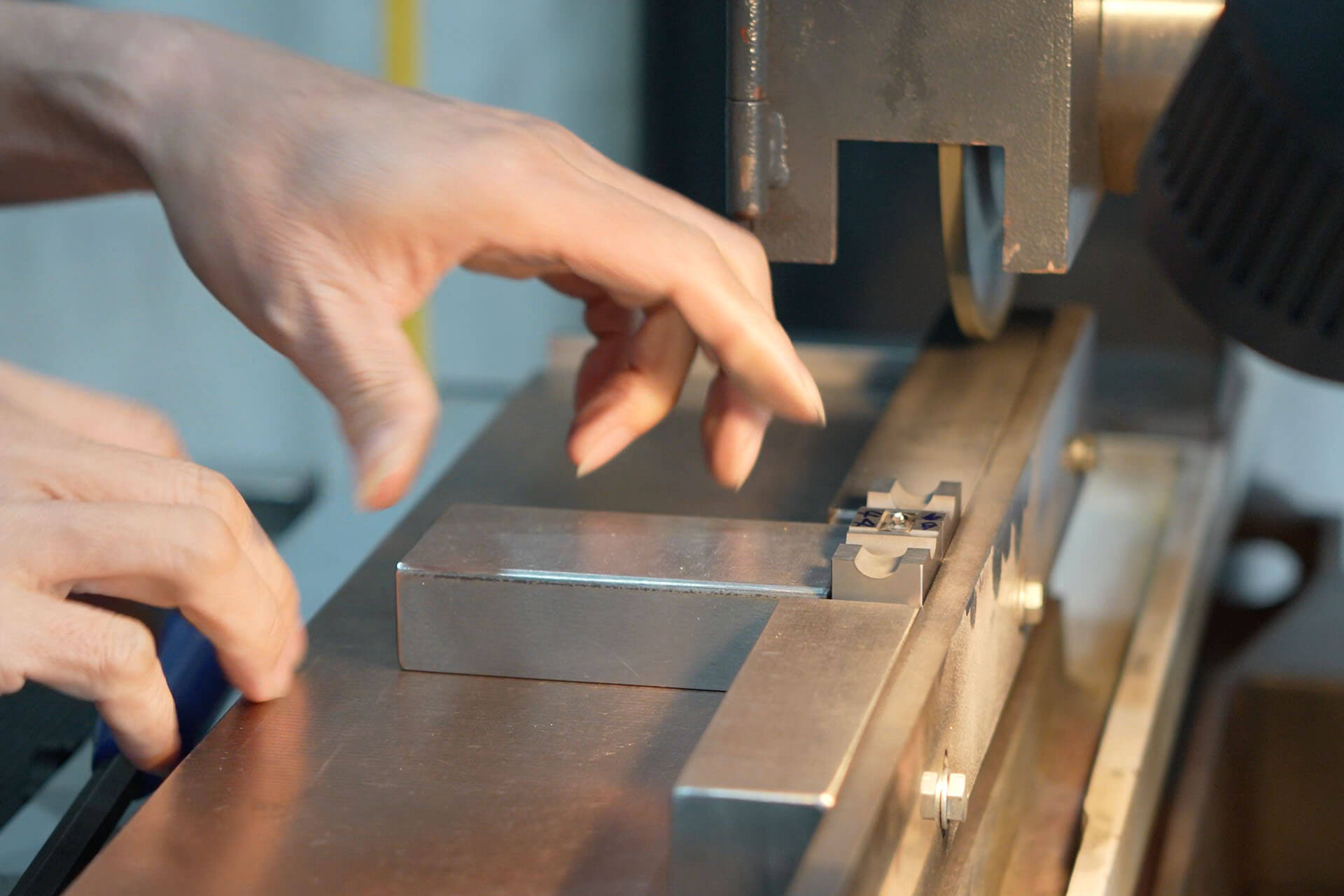
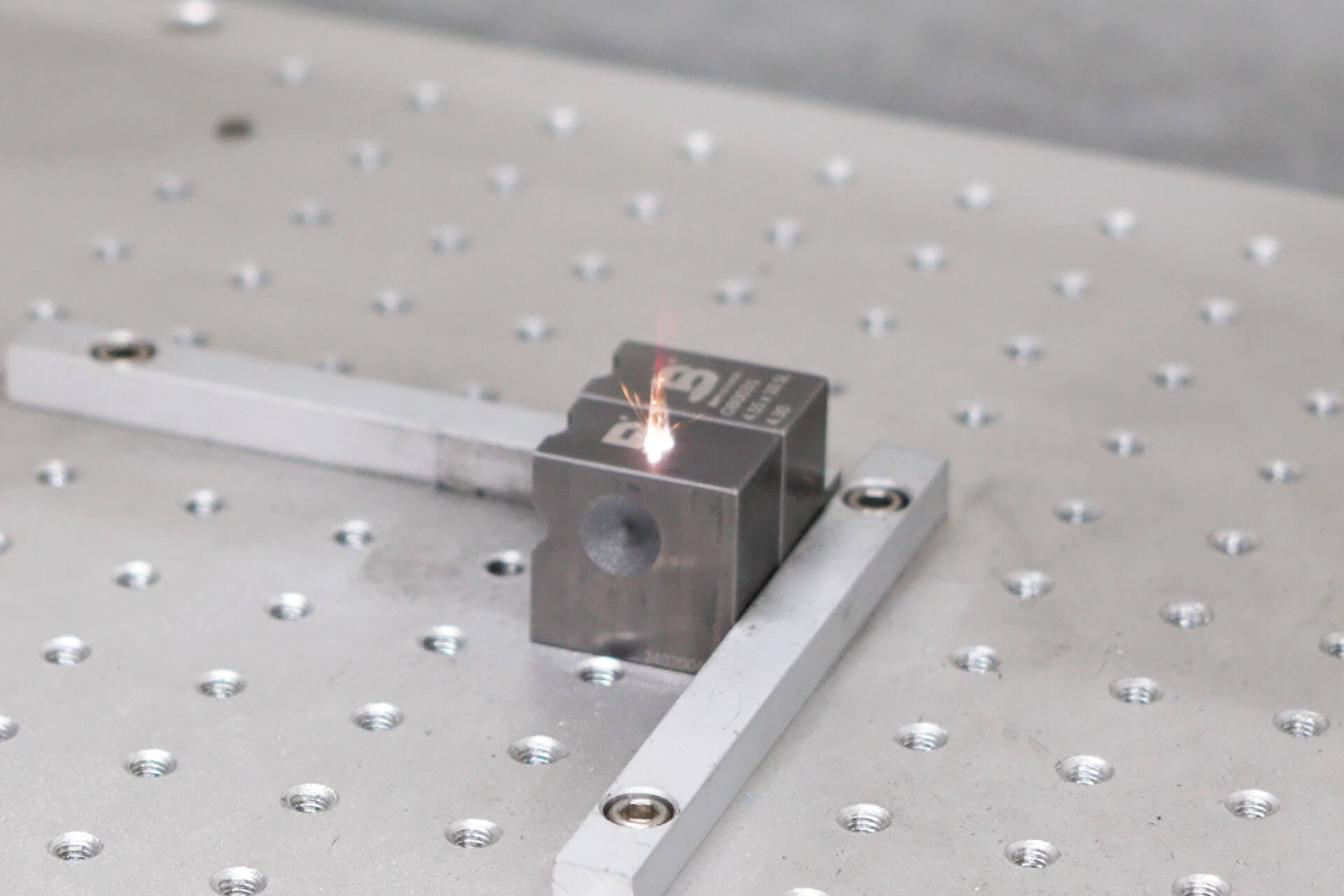
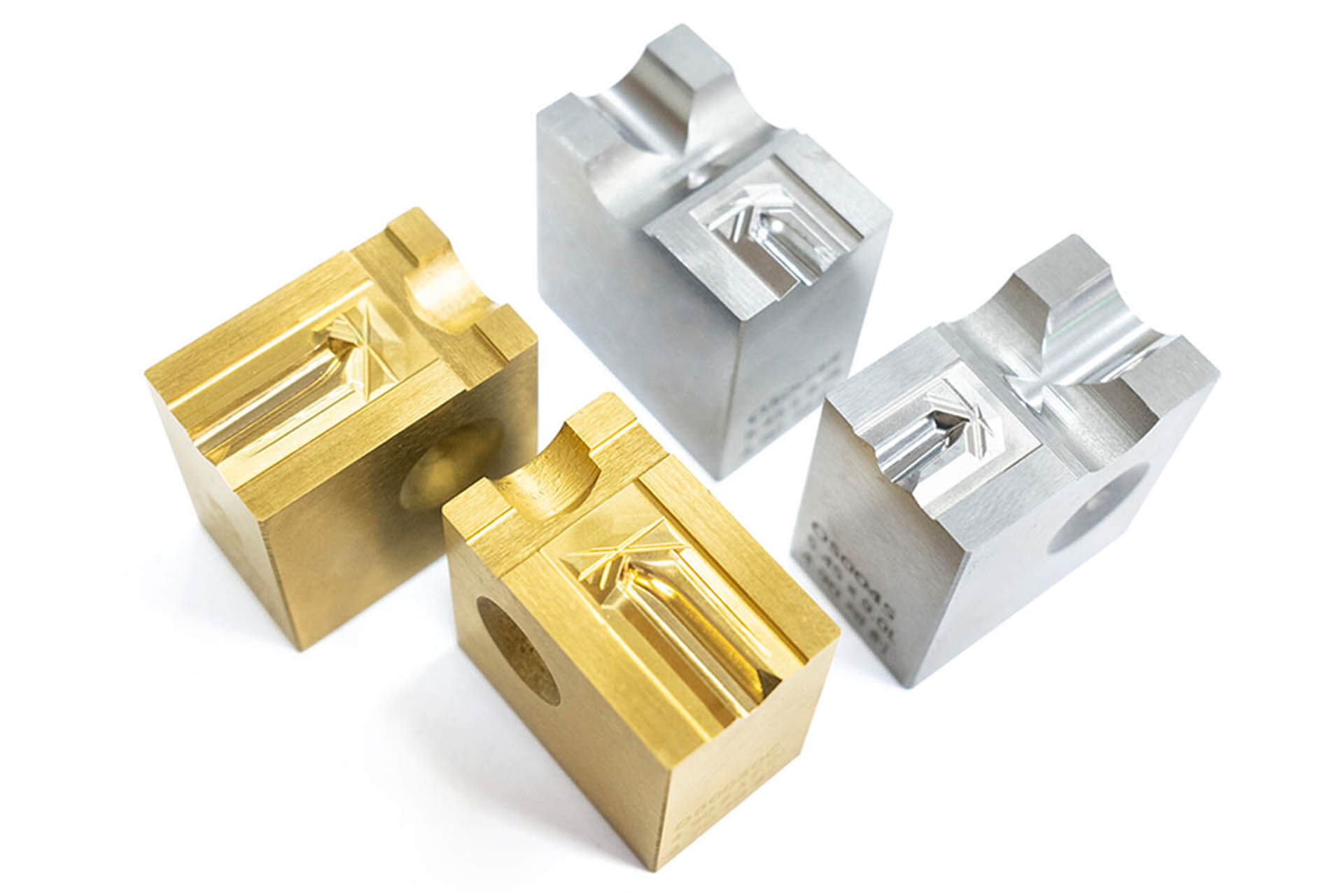
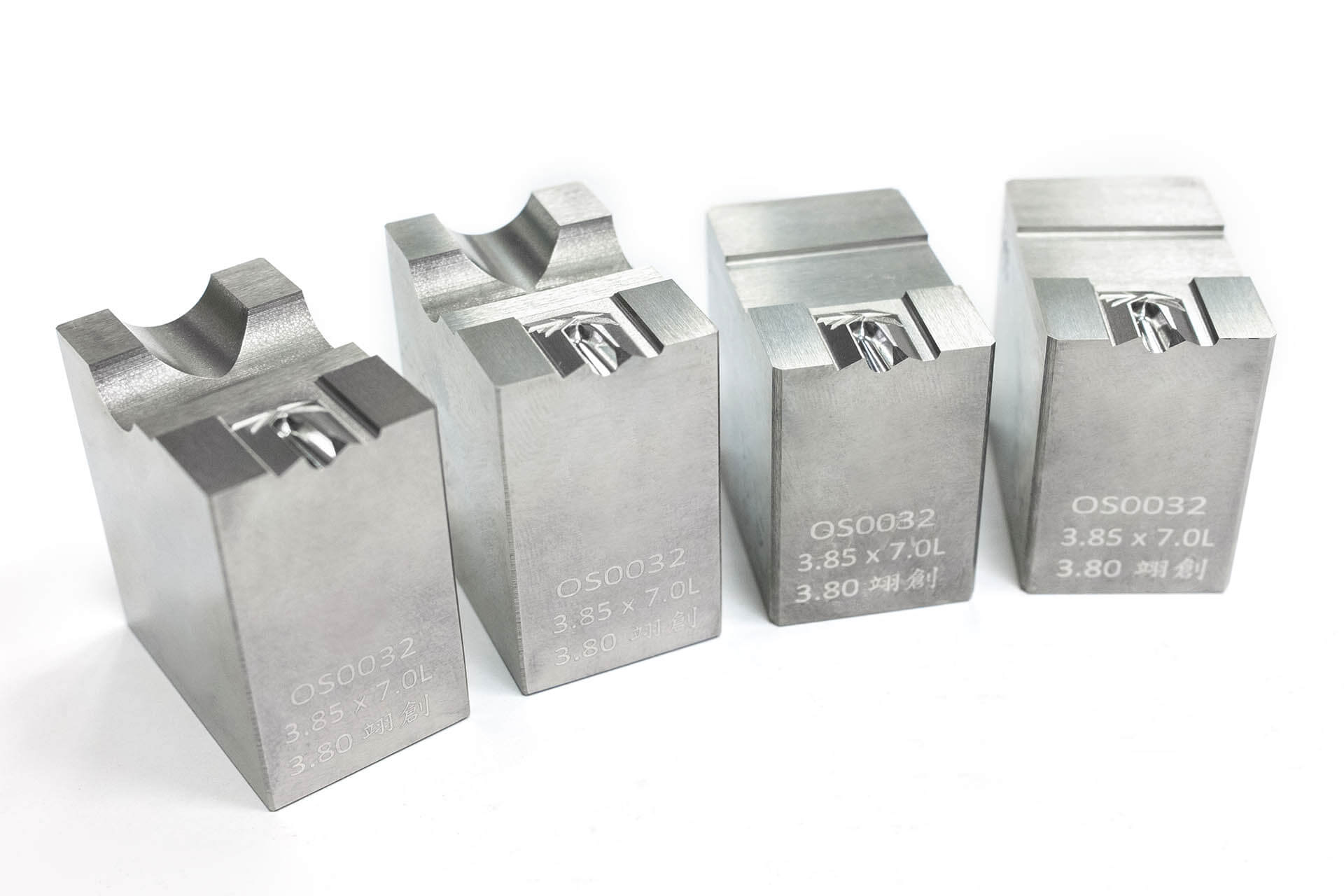
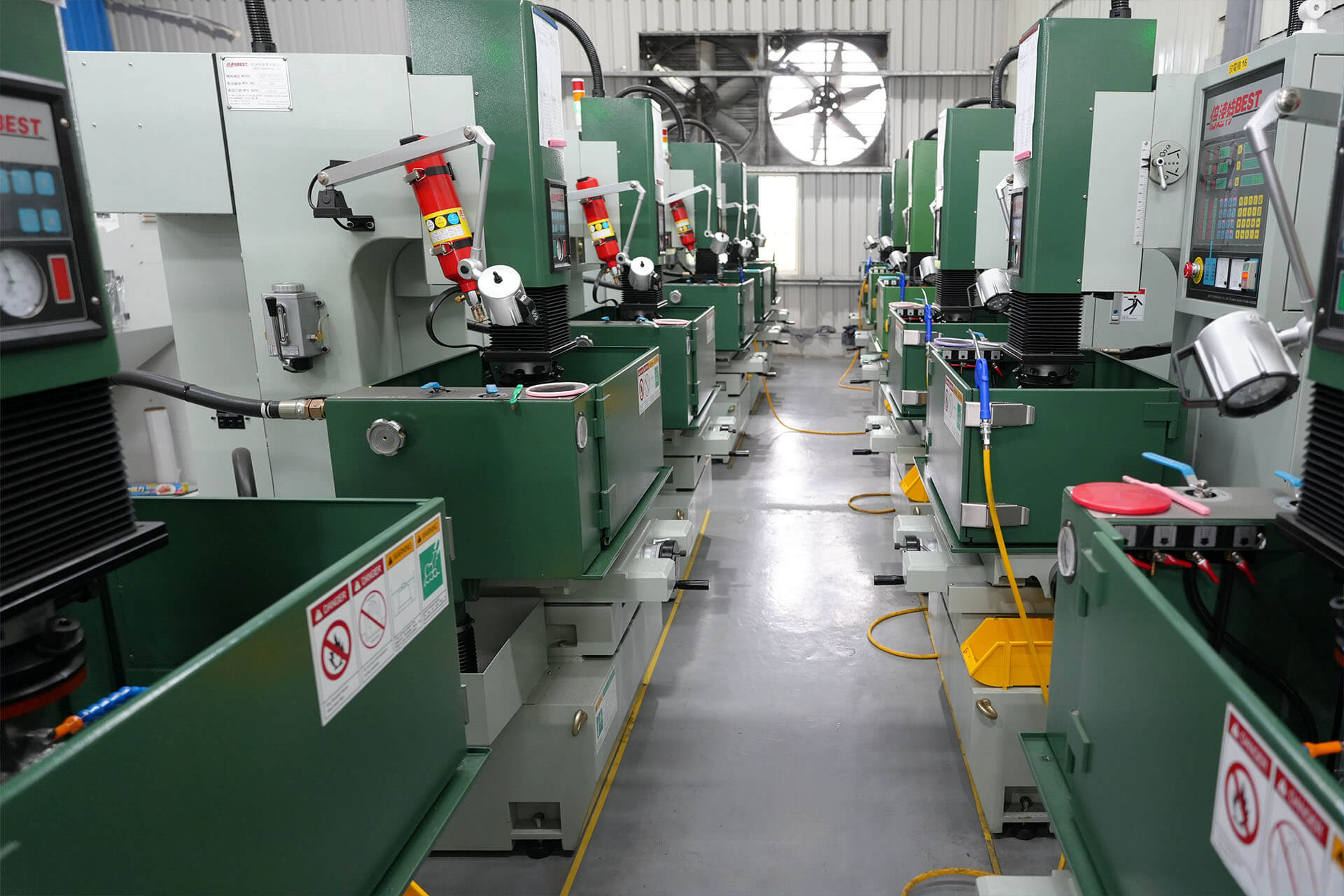
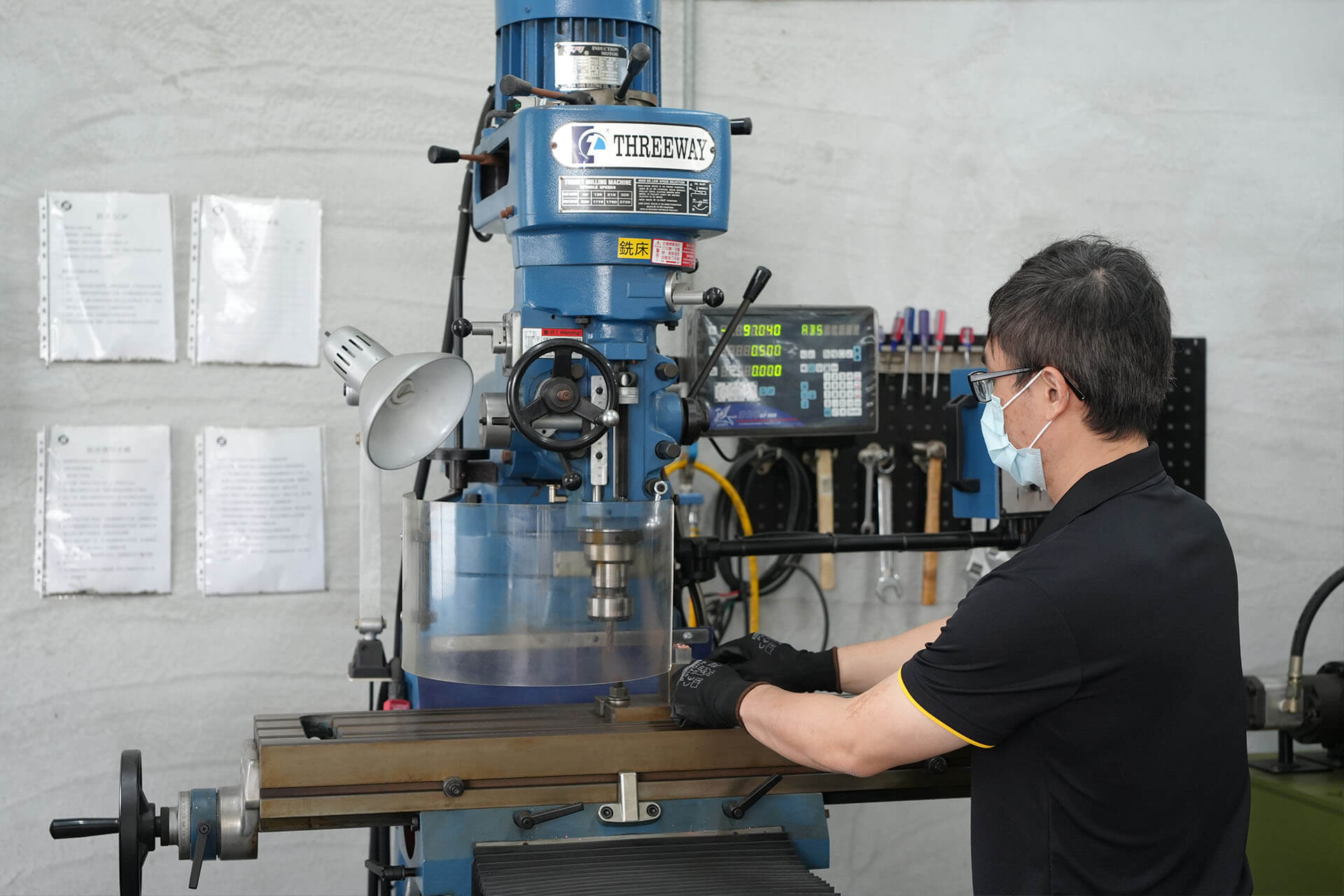
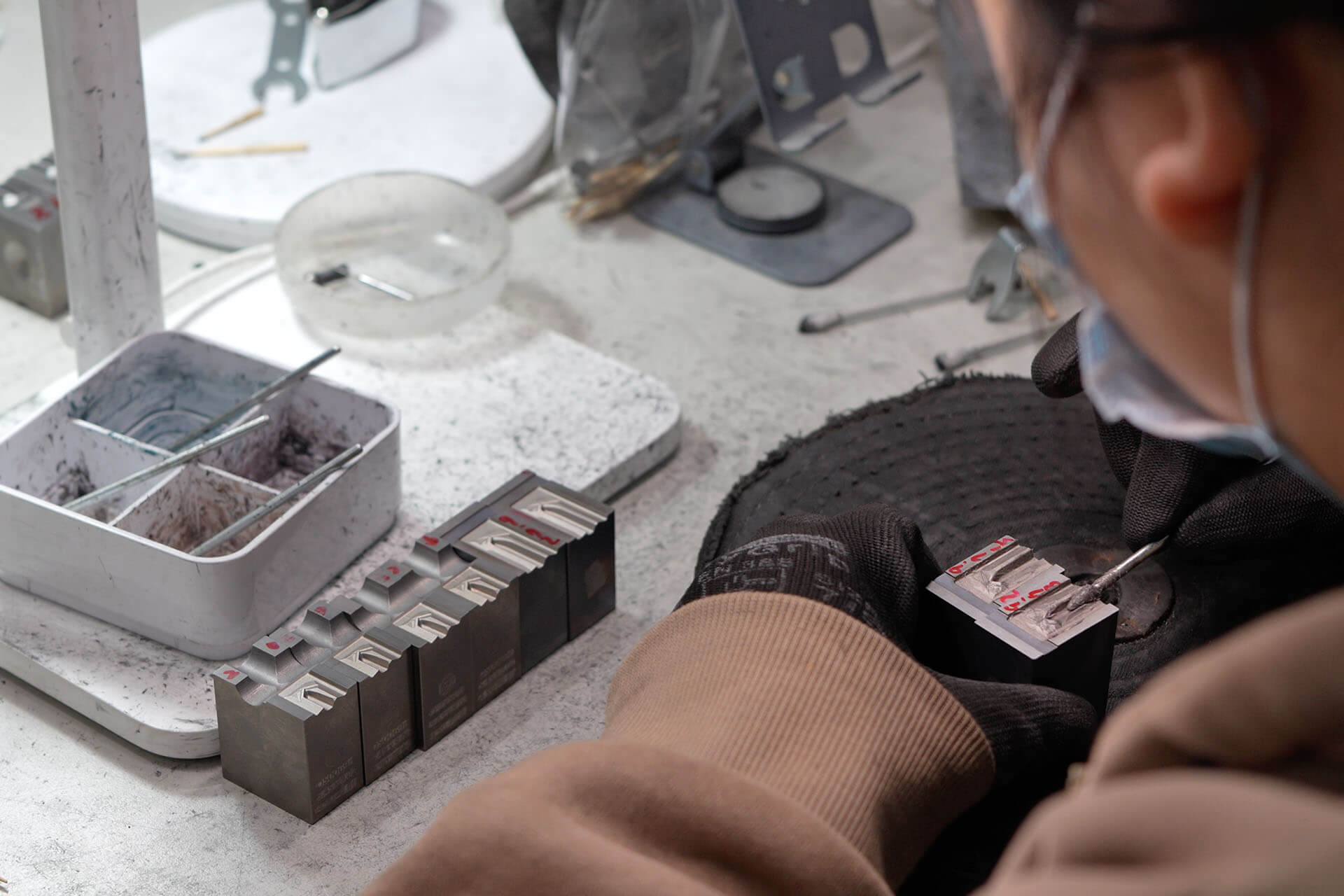